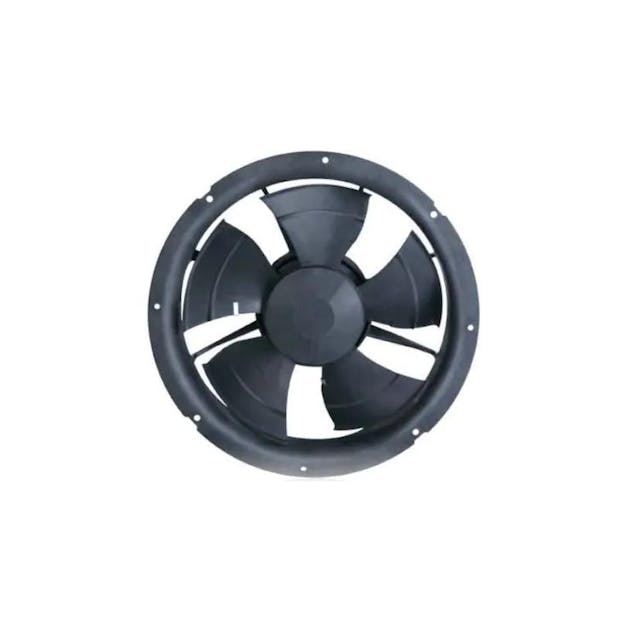
Fan AS-172
suction, propeller diameter: 172 mm, capacity: 400/960 m³/h, remote speed programming (NFC)
09/01/2023
Since the beginning of the HVAC industry, various types of motors have been used in it. They are used to drive fans, which are an integral part of this industry. The most popular solution to date has been alternating current (AC) motors. However, refrigeration, like any other industry, is developing and has to face newer and newer requirements: energy efficiency, ecology, comfort or increased accessibility for the user.
Refrigeration components such as fans also need to go a step further. Above all, there is a growing demand for quieter, more efficient and energy-saving operation. In turn, the development of fans is inextricably linked to the development of the electric motors that drive them. AC motors are more and more often replaced by an ECM motor (Electronically Commutated Motor), in short: an EC motor that combines the advantages of the popular, but too high energy demand, AC motors and DC motors, which drive most electronic devices .
Electric motors in the HVAC industry are used e.g. in condensers or evaporators to drive fans of all types: axial and radial. The most commonly available on the market are basic AC commutator motors. They offer different power values and rotational speeds. These motors must be adapted to work in a wide range of temperatures. An example of such a device is the Airvent AV-16-25 fan motor, 16W, adapted to work in temperatures from -25 oC to 50 oC. It is a cheap and quite reliable solution, but it does not give such large savings during operation.
An alternative, increasingly used solution is ECM motors, also known as BLDC motors (brushless DC motors), i.e. electronically commutated, brushless motors. ECM motors are characterized by greater energy efficiency, efficiency and reliability. Their operation is simpler, more convenient and gives greater control possibilities. For example, the ECM7108DW two-speed fan motor with a power of 7 W generates rotational speeds of 1300 and 1800 rpm. What's more, despite the higher purchase price, it is an investment that in a relatively short time can also bring measurable financial benefits resulting from limited electricity consumption.
The EC motor consists of several elements. Its most important elements include:
The stationary stator is inside the rotor. The motor also has a permanent magnet position sensor, most often a hall sensor. The sensor is responsible for transmitting information about the current position of the rotor to the electronic commutator.
An EC motor is a DC motor that is obtained by using a rectifier that converts AC voltage to DC voltage. When power is applied, current flows through the coils on the stator. This generates electromagnetic forces on their windings. The controller controls the motor so that the current always flows in the right direction through two adjacent coils. The direction of the current flow determines the polarity of the resulting electromagnet, and thus also the repulsive or attractive effect. In this way, the permanent magnet on the rotor is repelled from one coil and simultaneously attracted further to the other coil. After rotation, the driver directs the current flow to the next coil, thanks to which the permanent magnet, and thus the rotor, are in constant rotation. Information about the current position of the rotor, which is necessary for the correct activation of the coils, is collected by the Hall sensor and transferred to the controller.
Each electric motor uses electromagnetic forces to make the rotor rotate. The way in which this movement is achieved depends on the construction of the motor and the voltage connected to it (DC or AC).
In the EC motor, movement is achieved by electronically controlling the flow direction. The rotor is a permanent magnet and the stator with coils is an electromagnet. Thanks to the controller, the polarity of the electromagnet is constantly changing and thus rotation occurs.
In an AC motor, motion is achieved by commutator control of the direction of flow. Instead of electronics, we are dealing with brushes and rings. The stator is a permanent magnet, and the rotor is equipped with coils that turn into an electromagnet. The rotor is inside the stator, not outside like an EC motor. Thanks to the brushes connected to the rings, the current flows through specific coils.
In electric motors, repulsive and attractive forces arise between the magnet and the electromagnet. This is how rotation occurs. Of which the EC motor, thanks to the controller, gives the possibility of electronic regulation of this process.
The increased interest in electronically commutated motors is due to a number of their advantages:
Below we present data showing the working conditions of EC motors compared to traditional AC motors. The comparison compares the ECM7108DW motor with a power of 7 W and the Airvent AV-25-40 motor with a power of 25 W, generating the same rotational speed of 1300 rpm.
Assuming that the engine works 24 hours a day, 365 days a year, and the cost of 1 kWh is PLN 0.73, the ECM engine is able to save approx. PLN 115 per year compared to traditional engines. Which means that the higher purchase cost pays off quickly. And adding to this reliability, the engine saves money and energy during further operation, while contributing to the ecological operation of the entire refrigeration system. Considering the quoted data, it is worth considering replacing the AC motor with a brushless motor. The more so that the housing of EC motors is traditional and universal, which makes replacement easy and brings measurable benefits in the form of reduced power consumption.
EC motors are used e.g. in industrial automation, household appliances, small consumer electronics, or in the HVAC industry. Motors work best in devices where low rotational speeds are required, as this is when they achieve the greatest efficiency. Brushless motors work very well in refrigeration - as a fan drive, for refrigerated counters or industrial refrigerators. It is this working environment that contributes to their best performance - power demand from several dozen to several hundred watts and appropriate rotational speeds. The reliability of EC motors is particularly desirable in places that require its continuous operation. The construction of the motors guarantees high protection against moisture, it is specially dedicated to work in, for example, cold stores and industrial refrigerators.
EC motors work best with high-efficiency propellers, generating a limited noise level. These are propellers with plastic or steel blades. Propellers specially dedicated to cooperation with EC motors can be easily found in our company's offer. Their aerodynamics are adapted to the way the engine works, creating ideal working conditions for it. For example, a steel fan EC092/25E3G01-AB350/92S1-01-G, with an input power of 170 W, a diameter of 350 mm, generates noise of 67 dBA, while its greatest advantage is its efficiency, which is 3500 m3/h. The EC092/35E3G01-AS450/96P1-01-G fan, with a diameter of 450 mm, requires the same input power, generates the same noise level, and the efficiency increases to 5350 m3/h. EC motors are perfect for both axial and centrifugal fans. An example of such cooperation is the ECM-YGF60-180 centrifugal fan with very good performance.
suction, propeller diameter: 172 mm, capacity: 400/960 m³/h, remote speed programming (NFC)
suction, propeller diameter: 230 mm, capacity: 400/960 m³/h, remote speed programming (NFC)
suction, propeller diameter: 200 mm, capacity: 350/540/620/900 m³ / h, remote speed programming (NFC)
suction, propeller diameter: 300 mm, capacity: 2400 m³ / h
single speed 12W for condenser, evaporator, cooler
two-speed 7W for condenser, evaporator, coolers