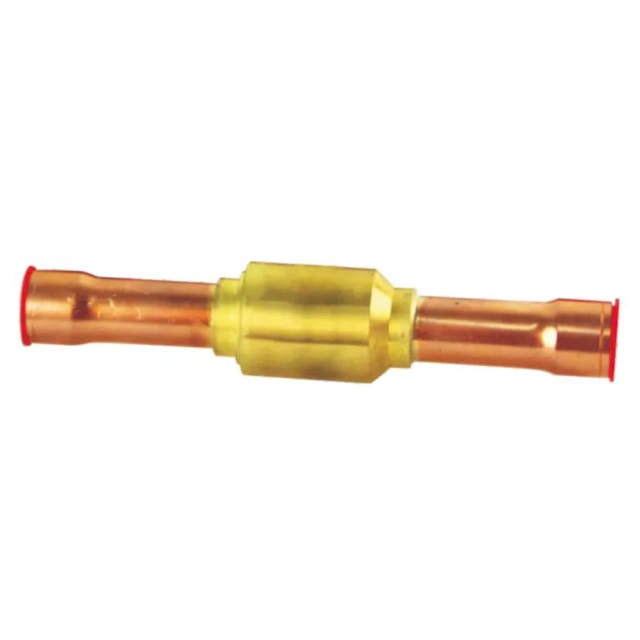
Check valve BLR/NRV-16S (5/8” ODF)
A globe valve, straight, brazed
They perform very simple, yet extremely necessary functions in various types of circuits and systems. A valve is a device used to close openings, outlets, to regulate the flow of media through conduits and to prevent their backflow. Types of valves available on the market, differing in application, size, construction or material from which they are made. Depending on the needs, they can change the angle of flow (angular valves) or leave it undisturbed (straight-way valves). In addition, valves in pressure systems are used to regulate pressure and control its release.
In the vast majority, the construction of valves is based on the same principles. Each of them has a socket with a flow hole. The next element of the valve is the gate valve, which is responsible for regulating the flow of the medium. The shape of the gate valve, depending on the application, may be in the form of a ball, piston or gate valve, and its control is carried out by means of a pin; it can perform, for example, rotational (ball) or reciprocating (piston, needle) motion. Both the flow seat and the shutter are located in the valve body.
Valve materials vary depending on their application. Metal alloys are most often used to build the body: brass, bronze and alloy steels. For valves operating at lower pressure, plastics and fiberglass reinforcements are used. In working environments that expose the valve to corrosion, such as sea water, alloy steels with high corrosion resistance are used.
In the refrigeration industry, valves are installed that are necessary for the proper operation of the system and those that, as additional elements, will increase safety or facilitate servicing and control. In a refrigeration system, we deal with the flow of refrigerant and gases through pipes. In such places, the valve is used to control and regulate the volumetric flow rates. In turn, in pressure vessels, of which there are also many in the refrigeration industry, such as refrigerant tanks, valves ensure safety. Their purpose is to open or close in case of inadequate pressure values.
Importantly, each of the valves must meet the criteria of high tightness, reliable operation under pressure and stainless steel. A very significant aspect of their work is also resistance to low and high temperatures. Below we have distinguished several types of valves most commonly used in refrigeration.
As the name suggests, a shut-off valve is used to completely shut off or open the flow. They are used in every refrigeration system. They facilitate the servicing of installation components and ensure its safety and enable the flow to be closed in the event of a failure. The most commonly used shut-off valves in the refrigeration industry are ball valves, rotalocks, safety valves and solenoid valves. And a description of these solutions can be found in the following section.
The ball valve is most often used as a shut-off valve not only in refrigeration, but also in any other industry. The name ball comes from the shape of the sphincter, which is responsible for regulating the flow and has the form of a ball with a hollow hole. Its rotation limits the flow of the medium. This valve can be used anywhere in the refrigeration system, however, it must be adapted to the pressure prevailing there to ensure maximum tightness. An example of a standard ball valve with two-way flow is the BLR/GBC-18 (3/4”) valve available in our offer.
This solution is for use as shut-off valves only and should not be used as regulating valves unless electrically or pneumatically operated.
An additional element of the ball valve can be the so-called gland. The gland in the ball valve is a more advanced form of sealing and a way to eliminate possible leaks.
We see ball valves both in larger industrial installations, as well as in houses and apartments. That is why it is worth knowing how to operate such a valve so that it serves us as long as possible. Not every failure of the ball valve will result in the immediate need to purchase and replace it with a new one. In some cases, it will be possible to repair the valve, which is discussed below.
Blocked ball valve
Blockage of the valve is most often caused by dirt or rust that accumulates over the years when the valve is in one position. In such a case, it should be started. To start the valve, unscrew the plastic handle to reveal the knob. They are operated with a flat wrench. After selecting the appropriate size of the wrench, make short movements with your hand, as if you want to unscrew the valve. After a few tries, the valve should begin to open and close smoothly. In the event that such action does not bring results, it is necessary to use grease or multi-purpose oil. Apply the oil to the top of the stem so that it flows into the valve by gravity. After applying the oil, wait several minutes for it to penetrate all the mechanisms well. This should make it easier for us to start the stagnant ball valve.
Leaking ball valve
A frequent failure of the valve is its leakage. In this case, the seals fail, which are undoubtedly one of the least durable components of the valve. Some valve variants have the possibility of replacing the seals. We can then unscrew the valve and replace the seals with new ones. Here it is worth noting that valves with a gland make this process much easier, because you only need to tighten the nut that is already built into the valve. In some cases, traditional sealing tow can be used. Such actions, however, are temporary and require checking to make sure that the leak problem does not return.
Unsealing of the ball valve
Temperature differences, manufacturing errors, or an improperly selected valve for the installation may contribute to the formation of cracks in the valve body. Even small fissures will propagate to larger defects over time. Such a valve should be replaced with a new one. However, if a temporary solution is needed, sealants, elastic adhesives can be used. They are applied in layers. They can restore the tightness of the body, but it is not a guarantee of work at the best performance and it is not a lifetime solution.
Rotalock is one of the most useful service - shut-off valves. It greatly facilitates all maintenance and replacement of units in the refrigeration system. The installation of a rotalock valve in the system is highly recommended, especially at the compressor. It is made of a plunger ended with a piston, which, when moved, cuts off the main flow and at the same time opens service access. Most rotalock valves have an additional port for connecting pressure gauges. Then we get accurate information about the compressor's operating parameters. This valve makes it easy to add and remove refrigerant from the system and replace the compressor. In our store's offer you will find a wide selection of such solutions, such as a rotolock valve with two service accesses BLR/RV-3/8.
As the name suggests, the role of the safety valve is to protect the system, for example, against exceeding the permissible high pressure, which may result in damage to the refrigeration system. This is counteracted by the safety valve, which, when opened, releases the medium until the pressure drops to a safe level. These valves can be used e.g. to protect compressors or tanks in refrigeration systems.
A solenoid valve is a special type of shut-off valve. It is controlled by an electromagnetic coil. Normally Closed (NC) valves cut off the flow of refrigerant when the coil is de-energized, and when energized the valve opens. Normally open (NO) valves work inversely, i.e. when no voltage is applied, the valve remains open. The NO valve closes when the coil is energized. The solenoid valve can act directly, which means that the force caused by the voltage will immediately open or close the valve; or indirectly, when the force activates the intermediate valve responsible for opening the main valve. Indirect-acting valves need a differential pressure between the upstream and downstream sides to open. This is the so-called servo control.
Solenoid valves are used in household, industrial and automotive installations. Solenoid valves are also necessary in refrigeration systems, e.g. on lines with high-pressure liquid refrigerant. Such solutions, suitable for the refrigeration industry, can be found, among others, in the offer of our warehouse. Among the proposed products are indirect and direct-acting solenoid valves or diaphragm solenoid valves, which use a diaphragm as a closing valve, which opens the flow of the medium by lifting it.
In addition to shut-off valves, check valves are another group of valves widely used in various types of installations, including refrigeration systems. The non-return valve allows the medium to flow in one direction only and blocks it in the opposite direction. It uses the pressure difference for this purpose. If there is a difference on both sides of the valve, the valve will close or open automatically. When the pressure values change again, the valve will return to its original position. The opening and closing of the check valve should take place immediately after the appearance of the pressure difference.
This valve uses a spring-loaded plunger to regulate flow. Its operation depends on the pressure in the lines. When the pressure pushes on the piston from the right side, it will rise and open the flow. However, when the pressure appears on the other side of the piston, i.e. the medium will want to "return", the piston will move down, cutting off the flow, thus ensuring a continuous, appropriate direction of flow.
Valves should be selected for the system depending on the cooling capacity, not according to the diameter of the connection. They are placed, for example, in devices where the factor and its vapors are stationary, when the flow is particularly exposed to changing its direction. It is very important that it is installed in the direction of flow. In addition, a special type of non-return valve, i.e. a non-return valve, can only be installed horizontally, which results from the specificity of the construction of the non-return valve.
The control valve allows us to control the flow volumes of the medium. These valves are often used with automatic regulation, so that we do not have to constantly control the flow parameters. Automatic control systems control the control valve depending on the current pressure, temperature and other parameters that are important to us. On the other hand, manual adjustment allows you to quickly change the volume when you need it.
An example of a control valve is an expansion valve. It is placed between the filter drier and the evaporator. Its task is to regulate the flow of refrigerant to the evaporator. The expansion valve, compared to other valves, performs a special function, namely it lowers the pressure (hence the name expansion valve). As a result of the pressure drop, the temperature of the refrigerant also drops significantly, to a level that allows its complete evaporation in the evaporator.
The Shrader valve looks a bit different from the other refrigeration valves discussed so far. With this valve, you can regulate the amount of medium in the system, it does not interfere with its flow. Most often we find it in the form of a valve, in all kinds of tires. It consists of a cylinder in which a tube resting on a spring is placed. The tube is equipped with a gasket which, by pressing it against the spring, blocks the flow of the medium. The valve opens by pressing the tube. Shrader valves are also used in refrigeration. Namely, they provide service access to wires and devices and allow refilling or removing the refrigerant from the installation. In industry, you can come across a wide variety of diameters and dimensions of valves.
Valves, despite the fact that they look inconspicuous, perform the necessary functions in installations. Their failure can cause us a lot of trouble and cost us a lot. Therefore, it is important that their exploitation is at a high level. Key points to keep in mind:
Proper installation. Always ensure that the person responsible for installing the valve is a specialist in their field. A well-chosen and installed valve guarantees its longer life and no surprises such as leakage or cracks in the body.
Cleaning and lubrication. Regular removal of impurities from the valve body reduces the risk of them getting inside and seizing moving parts. You can clean it with an ordinary cloth, using basic cleaning agents. It is worth making sure that they will not react undesirably with the material from which the valve is made. In addition, lubrication of the valve ensures its smooth operation, supports seals and reduces the risk of valve sticking. It is a good habit to perform such services at least once a year.
Regular inspections. It is worth inviting a specialist to check the correct operation of the entire installation, including valves. It will check the stability of the assembly, proper tightening of the elements, the risk of leakage or cracking.
A well-chosen and operated valve should not surprise us with a failure that will force the entire installation to stop working. It is not worth saving on the quality of these elements to be sure that we will not be exposed to losses caused by destruction. If you are looking for high-quality valves that are tailored to the needs of service technicians and installers, we encourage you to familiarize yourself with the offer of our refrigeration warehouse. If you have an additional question, please contact us.
A globe valve, straight, brazed
Globe, angle, brazed valve
with Schrader service valve, for bidirectional flow
service connection with 6mm SAE thread
angular
soldered, normally closed
screw connection (1/2' SAE), normally closed
soldered