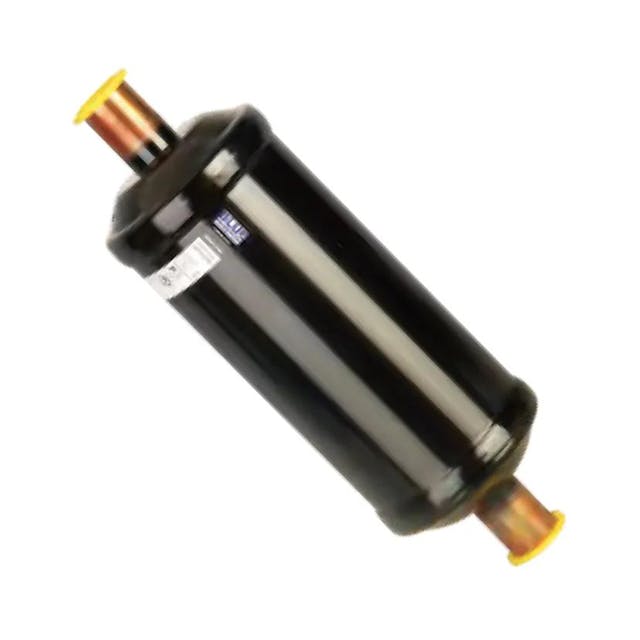
Filter drier BLR/DML-305 (5/8” SAE)
with 100% solid core with molecular sieve
A filter drier is an important component of any refrigeration and air conditioning system that should be used in both industrial and commercial systems.
The main tasks of filter driers are to protect the system against moisture, acids and solid impurities. Their use effectively contributes to improving the efficiency of the system and reduces the risk of failure of the refrigeration system. In this post, we will try to discuss the most important issues related to the use of drainage filters.
The presence of moisture in the refrigeration and air conditioning system is an undesirable situation, because it can lead not only to a decrease in system efficiency, but also to the failure of the refrigeration system. What can be the effects of the presence of moisture in the system we will discuss in a moment. First, let's determine what may be the reason for its appearance in the system.
The most common sources of moisture in a refrigeration system include:
Moisture in the system is one of the most common causes of refrigeration system failure. Let's take a look at what the effects of its presence can be. The first example of problems related to moisture in the refrigeration system may be its negative impact on the operation of the compressor. In the compressor, problems due to residual moisture in the system will be the oxidation of metal components and the degradation of the oil from the active ingredients produced by mixing water with oil. Oil in combination with moisture loses its lubricating properties, the consequence of which is seizing of elements in the compressor and higher energy consumption, which can even lead to compressor burnout. In addition, water that appears in the system can react with polyester lubricants, resulting in the formation of organic acids. The situation is not facilitated by the fact that POE is a hygroscopic substance, i.e. it easily absorbs moisture. Another undesirable consequence of the appearance of moisture in the refrigeration system may be the freezing of water in the expansion elements. As a result of water freezing in the expansion elements, the moving element is blocked, which makes it impossible to regulate the flow of the medium to the evaporator. In turn, the lack of such regulation may lead to liquid refrigerant entering the compressor (destroying it) or poor heat reception in the evaporator (temperature will be higher than assumed).
The above examples illustrate how undesirable moisture is in the refrigeration system. In order to protect the system from the effects of moisture, it must be effectively limited. This is possible thanks to the use of a filter drier, which ensures that the system is kept dry and clean. The filter drier is an effective way to protect the system against moisture, acids and solid contaminants.
Filter driers should be installed just after the condenser to ensure that the flow is single phase and the refrigerant is cleaned properly. Most filter manufacturers allow any orientation for mounting the filter drier. This is also the case with Blue Refrigeration filters of the BLR/DML, BLR/DCL and BLR/EK series. However, it is still recommended to install it so that the filter drier is placed in an upright position and the condenser inlet is in the upper connection. The option of vertical installation of the filter drier is especially worth considering in the case of BLR/EK series filters. This recommendation is due to the fact that the filling of these cartridges is an absorbent substance in the form of granules (and a filter responsible for separating solid particles). In the case of horizontal installation, we run the risk that the granules will not be properly compressed and the refrigerant will find a bypass through the resulting gap between the grains and the housing.
As already mentioned, the filter drier should be installed in the liquid line, before the expansion valve, so that the water does not freeze due to a sudden drop in pressure and temperature. It is equally important to avoid installing the filters in places where they would be exposed to external heat loads. This is due to the fact that the water absorption capacity of the filter drier also depends on the temperature. When installing the steam trap, the seals at the ends of the steam trap should be removed just before connecting the filter drier to the rest of the installation to avoid water absorption from the air through the trap core.
When the system is in operation, the filter drier can, due to excessive moisture and dirt loading, cause pressure drops, which lead to a decrease in the efficiency of the entire system. In this situation, a liquid sight glass with a humidity indicator will be a helpful device, which should be mounted on the liquid line after the filter drier. With its help, we can initially assess the condition of the refrigeration system. The liquid sight glass allows you to observe and evaluate the condition of the refrigerant. Bubbles or foam may indicate insufficient refrigerant, but it may also be due to excessive pressure drop, which should be a sign that the filter drier needs to be replaced. On the other hand, the humidity indicator allows you to determine the degree of humidity of the system by changing the color of the indicator. The green color of the indicator indicates that the refrigerant is free of moisture (the refrigerant is dry), i.e. its condition is correct. The yellow color of the indicator means that the medium is moist. In this case, it is necessary to replace the filter drier with a new one.
Zacznijmy od tego, że każdy filtr odwadniacz ma swoją żywotność. Właściwości higroskopijne filtra osuszacza wynikają z jego wielkości, jak również zależą od rodzaju wypełniania wkładu (różnice między nimi omówimy w dalszej części). Nie zmienia to faktu, że filtr odwadniacz w układzie chłodniczym powinien być wymieniany przynajmniej co 2 lata, ponieważ po takim okresie eksploatacji wkład nie będzie w stanie skutecznie absorbować wilgoci. Jednocześnie konieczność wymiany filtra odwadniacza może być spowodowana również przez inne czynniki i zdarzenia, jak na przykład wystąpienie nieszczelności układu. Jednym ze sposobów monitorowania wydajności systemu chłodniczego, a tym samym prawidłowej pracy filtra jest obserwacja wziernika cieczy (co omówiliśmy wcześniej). Jakie inne sygnały i nieprawidłowości w pracy układu chłodniczego mogą świadczyć o tym, że konieczna jest wymiana filtra odwadniacza?
In order to choose the right filter drier, which will ensure proper and trouble-free operation of the refrigeration system, the following should be taken into account:
We would like to discuss the last of the mentioned elements, i.e. the type of filling of the filter drier. Molecular sieve and aluminum oxide are among the most commonly used fillers in filter driers.
The first of these, i.e. a molecular sieve, is a granulate with a very porous surface. The pores (equally sized cavities) have the ability to trap particles smaller than their volume, including water particles, while allowing the free flow of refrigerant and oil particles that are too large to be trapped. Thanks to this, the molecular sieve effectively absorbs water, minimizing moisture, and thus the possibility of acid formation in the system.
The second material used as the composition of the filter drier is activated alumina. This material is designed to neutralize organic acid particles that may appear in the system as a result of the reaction of water and POE lubricants. Trap cartridges with a high content of activated alumina are most often used in systems where a compressor burnout has occurred.
An example of a standard drying filter can be Blue Refrigeration BLR/DML series cartridges. Each filter drier in this series is equipped with a cartridge made of 100% molecular sieves. This solution effectively protects the system against moisture, and thus protects it against corrosion, oil degradation or other more serious failures. The second, equally popular type of filter driers are cartridges, which in addition to the molecular sieve also have active alumina. In the case of BLR/DCL series filters, the proportion of 80% molecular sieve and 20% active alumina is maintained, which allows not only to keep the system dry, but also to effectively absorb the resulting acids.
We have already touched on this issue when discussing the types of cartridges in filter driers. Due to its properties, the filling that is best suited for use in this case is activated alumina. An example of this type of filter drier are all DLR/DAS series dryers, whose core consists of 70% aluminum oxide and 30% molecular sieves. This solution allows both for effective separation of the acid resulting from the combustion of the compressor and moisture that could appear in the future during the operation of the system.
Filtr odwadniacz z wkładem wymiennym, określany również jako filtr składany, jest rozwiązaniem najczęściej wykorzystywanym w przypadku dużych instalacji chłodniczych, ponieważ wyklucza konieczność wymiany całego filtra. Przykładem takiego rozwiązania są wkłady serii BLR/STAS, których elementem wyróżniającym jest zdejmowany kołnierz, zapewniający łatwe czyszczenie, kontrolę oraz wymianę wkładów
with 100% solid core with molecular sieve
with 100% solid core with molecular sieve
with O-ring connection for car air conditioning
with 100% solid core with molecular sieve
with 100% solid core with molecular sieve