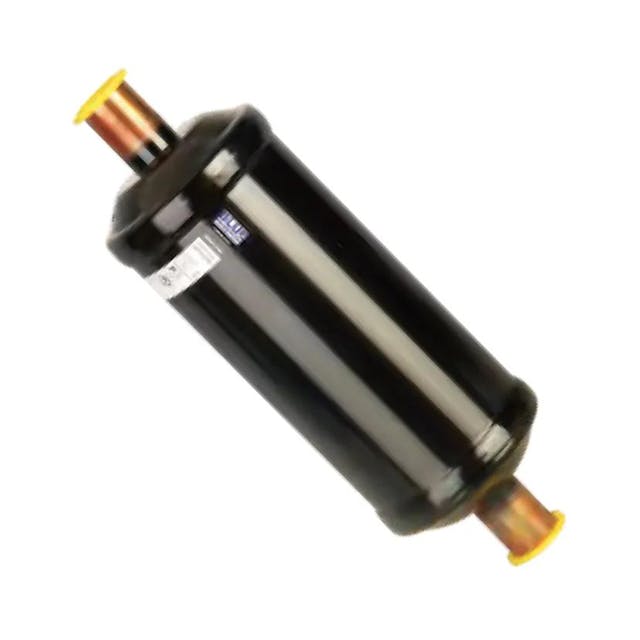
Filter drier BLR/DML-305 (5/8” SAE)
with 100% solid core with molecular sieve
05/09/2022
The filter drier is a very important element of the refrigeration system. It allows for separation of solid particles, moreover absorbs moisture and neutralizes acids in cooling systems. However, keep in mind that filter driers have limits on their absorbency. This means that each filter drier can absorb only a strictly defined amount of moisture and exceeding it may have a negative impact on the operation of the system.
The efficiency of the filter drier depends primarily on its size and the cartridge (type of filling), which is designed to absorb the moisture generated in the system. It is assumed that the filter drier should be replaced with a new one at least every 2 years. However, there are times when the presence of moisture in the system is so great that the filter will reach its maximum absorption limit before this time and is not able to effectively absorb the next portion of moisture. We most often encounter such cases because of improper handling of polyester greases (POE), improper filter installation technique, leaks in the system and motor winding, or improper service of the system.
A clogged filter drier, which is not able to effectively absorb moisture from the system, may have a negative impact on the proper operation of the entire system and cause several undesirable phenomena. In this post, we first list symptoms that may indicate a partially clogged water separator filter. Then we will try to explain how they happened.
Symptoms of a partially clogged drier filter include:
When the filter drier is clogged, we can observe several consequences from such a malfunctioning system. The first symptom on the list is a decrease in evaporator efficiency. Of course, there can be many reasons for this, and it is often related to a leak in the system, and thus too little refrigerant. At the same time, the effect of filter drier failure (clogging) is like the symptoms caused by too little refrigerant in the system. Lack of refrigerant causes more overheating of the vapor leaving the evaporator, as well as a clogged filter. The difference between the two failures is the subcooling on the condenser. If the subcooling value is greater than the design assumption, there is too little refrigerant. If the subcooling is what it should be (with high superheat at the same time), the problem is with the liquid line.
A clogged filter causes significant flow resistance, preventing the refrigerant from flowing freely. Refrigerant penetrating through the clogged filter undergoes a possible expansion, which is associated with a drop in pressure and temperature. The drop in pressure can cause the temperature at the outlet of the filter and in the filter to drop so much that condensation from the air or even frost can be observed on the liquid line. If significant differences in temperatures upstream and downstream of the filter are observed, the filter must be replaced without fail.
The cooled refrigerant then goes to the TEV which maintains a constant differential pressure between the liquid line and the inlet line to the evaporator, so if the upstream pressure drops, the downstream pressure also drops causing the evaporator pressure to drop. (An uncontrolled pressure drop across the evaporator can also cause a dirty heat exchanger.) The limited amount of refrigerant flowing through the evaporator causes more superheat leading to a higher suction temperature of the compressor. A consequence of this phenomenon is a significant increase in isentropic compression temperature. The result can be a very high temperature on the high-pressure line and an increase in the temperature of the compressor itself. In this case, it is likely that the compressor will be switched off by the low-pressure relay when the low pressure is reached. This will result in frequent switching on and off the compressor until the failure is repaired.
The volumetric capacity of the compressor, regardless of thermodynamic changes in the refrigeration system, remains constant. The increase in superheat causes the specific volume to increase, thereby reducing the mass flow. In this case, we can see a decrease in power consumption on the compressor, because it simply has less refrigerant to compress. Such a phenomenon may even increase the COP, but it must be remembered that it is a cost of lowering the cooling capacity.
The drop in evaporator cooling capacity due to insufficient refrigerant in the low-pressure line also causes the pressure in the condenser to drop. This is because the heat load contained in a given amount of refrigerant is reduced.
As a result, when the flow of refrigerant is significantly limited or not, the entire amount will be in the liquid accumulator, therefore it is recommended to remember when selecting this container that the total volume of the refrigerant is 70% of the liquid accumulator.
with 100% solid core with molecular sieve
with 100% solid core with molecular sieve
with 100% solid core with molecular sieve
with 100% solid core with molecular sieve
with O-ring connection for car air conditioning