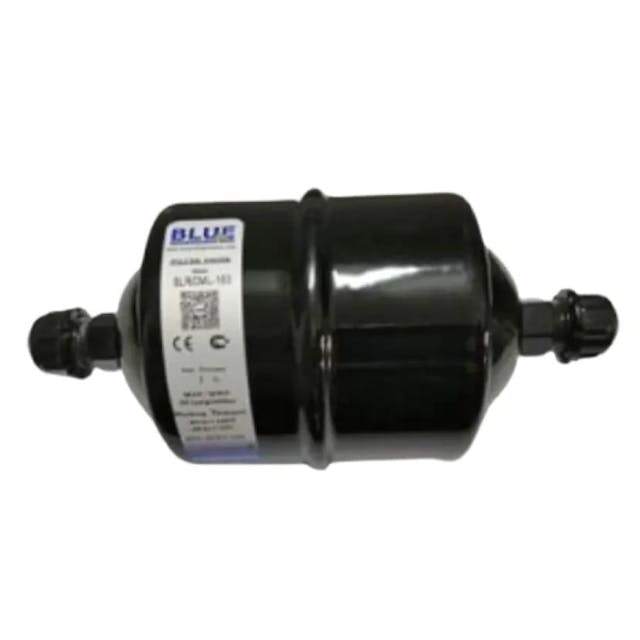
Filter drier BLR/DML-032 (1/4” SAE)
with 100% solid core with molecular sieve
12/06/2022
The filter drier is a key component of any refrigeration and air conditioning system. The function of the filter drier is to ensure high efficiency of the cooling system and minimize system failure. Therefore, these filters should be used both in commercial systems and in industrial cooling installations.
The main task of the filter is to ensure that the cooling system is dry and clean. Filter driers are responsible for retaining moisture and solid contaminants in cooling systems.
Various types of contamination that may appear in the refrigeration system pose a threat to parts that require high precision, such as compressors and expansion elements. Moisture can cause the formation of acids in the refrigeration system or deteriorate the lubricity of the oil, leading to compressor corrosion or seizure. In the case of the expansion element, the low temperatures occurring in it favor the freezing of the moisture, thus blocking the flow of the medium into the evaporator. As a consequence, the performance of the refrigeration system may drop.
Moisture and contamination can get into the refrigeration system as a result of loss of tightness during assembly, failure or servicing of refrigeration devices. Therefore, it is so important for many years of failure-free operation of the refrigeration system that the fitters and service technicians attach particular importance to ensuring the tightness of the installation, proper vacuuming before filling it with the refrigerant, using the filter drier and replacing it, so that the maintenance of refrigeration equipment does not involve any risk. air entering the serviced system.
Typical elements of filter driers are:
The refrigerant enters the filter through the inlet connection, then flows through the filter element and filter mesh, where moisture and impurities are trapped, accompanied by a drop in its pressure. It finally flows out of the filter through the perforated plate and outlet connection. Over time, due to the accumulation of moisture and/or dirt, the filter loses its drainage capacity. A clogged filter also causes an excessive drop in refrigerant pressure. It then needs to be replaced.
To properly select a filter drier that will keep your refrigeration system functioning properly and safely, you need to consider:
The choice of element composition affects the compatibility of the filter drier with the refrigerant and oil present in the system.
The use of a filter incompatible with the refrigerant or oil may result in the formation of acids, which pose a threat to the correct operation of the installation.
with 100% solid core with molecular sieve
with 100% solid core with molecular sieve
with 100% solid core with molecular sieve
with 100% solid core with molecular sieve
with O-ring connection for car air conditioning